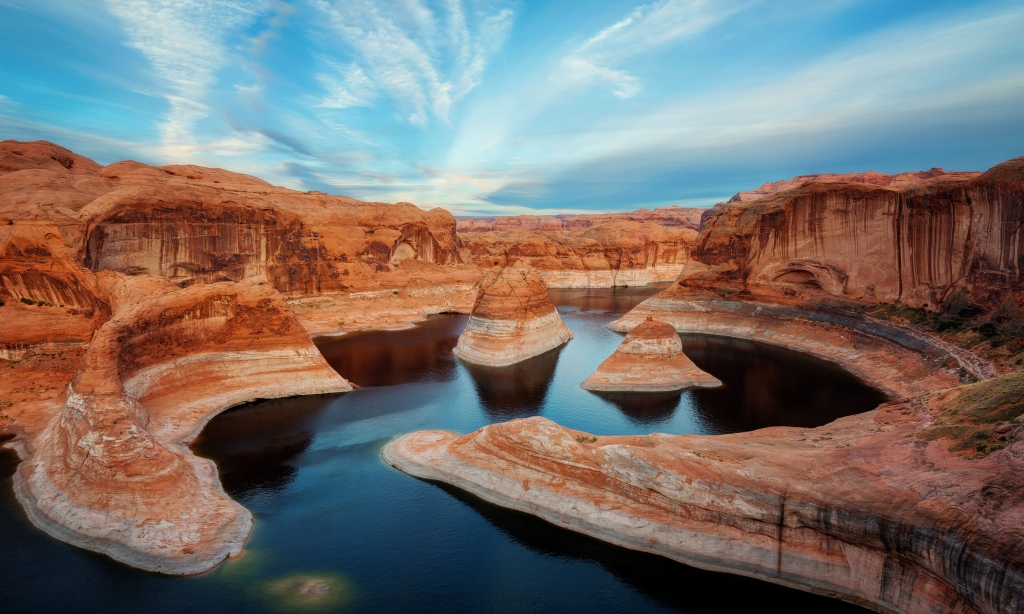
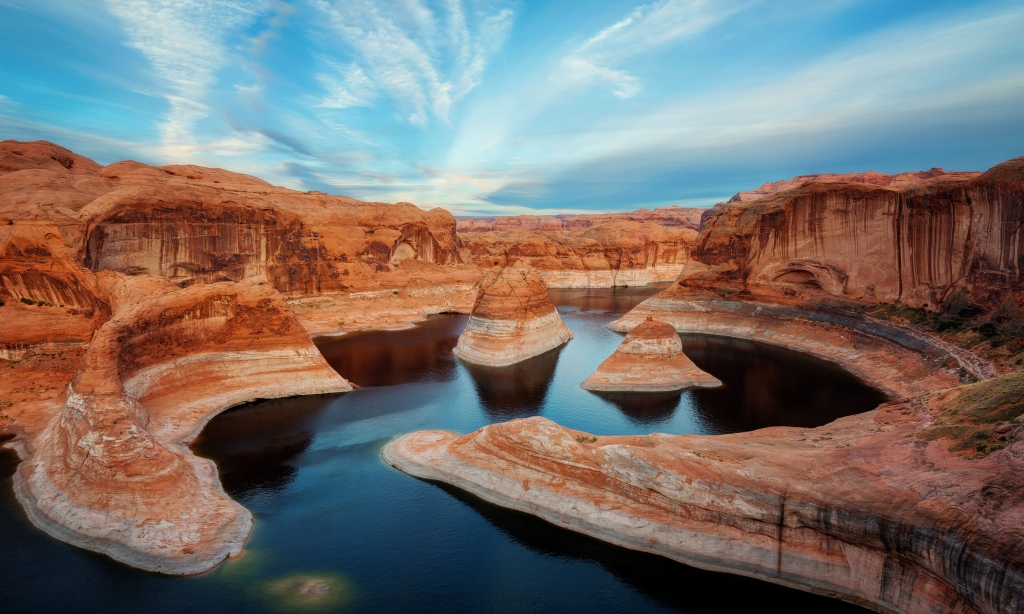
Written by
For years, U.S. food supply chains have systematically embraced Lean principles: complex systems and processes designed to optimize operations by eliminating waste and inefficiencies. These sophisticated models have worked remarkably well, creating significant value for the end consumer. For example, families are spending a full 8 percent less of disposable income on food today than they were 30 years ago — welcome news to the average household.
Nonetheless, concerns about optimization have been growing. Undoubtedly, these systems and processes work well in “normal” times; they can withstand day-to-day variations in supply and demand and routine uncertainty — a delivery truck breaking down, say, or an unexpected surge of demand for a certain product. The problem is that they are not set up to deal with big shocks.
As more and more manufacturing and logistics activities are outsourced, the management of supplier and customer relationships becomes increasingly complex and interconnected. Playing around the edges, looking for incremental efficiencies is great if your input remains the same — if the environment remains stable. But the moment there is any kind of severe variability in supply, optimization can bring fragility. Food shortages have accompanied some of the biggest natural disasters of the 21st century — extreme weather events, earthquakes and tsunamis, the SARS outbreak of 2002 — pointing to a systemic lack of resilience to major disruptions.
Lean, by definition, requires all nodes in the supply chain to operate synchronously. When its execution is focused exclusively on efficiency during “normal” times, it can become a problem when there’s a shock to the system. And a big problem, at that.
Even before headlines around the world became fixated on daily infections and death rates, the impact of the COVID-19 pandemic was becoming clear in grocery stores in the U.S. and overseas.
Within the first months of 2020, a national sense of panic had spread across the U.S. As household essentials from toilet paper to basic food supplies began to disappear from shelves, people started asking critical questions, and an unpalatable conclusion became increasingly likely: Something was seriously wrong with America’s supply chains.
Nowhere was this more evident than in the U.S. meat packing industry. On 26 April 2020, John Tyson, chair of Tyson Foods, took out a full-page ad in The New York Times. “The food supply chain is breaking,” stated Tyson. The impact of the pandemic on the company’s workforce, he went on, had been catastrophic. With workers falling ill or refusing to come to work for fear of infection, numerous meat plants across the country had been forced to close. Millions of pounds of meat would disappear from the supply chain, Tyson said. Meanwhile American farmers would have nowhere to sell livestock, meaning that millions of animals would have to be slaughtered. Products would remain in limited supply in grocery stores until the company could reopen their facilities, he warned.
Tyson’s predicament was unprecedented. But it was by no means unique. Across the U.S., scores of food producers were forced to close plants and factories as infections surged and the death toll continued to rise. On 2 June, USA Today reported more than 20,000 cases of COVID-19 at 216 meatpacking plants in 33 states. By September, The Washington Post had confirmed more almost 43,000 infections and at least 203 deaths. COVID-19 had been discovered in 494 U.S. plants.
The impact of the 2020 coronavirus pandemic on America’s meat industry laid bare an alarming lack of resilience in the food supply chain. It also revealed weaknesses in a particular area of sourcing that had historically been ignored or overlooked: human beings.
In “normal times,” meat plants such as Tysons are resilient enough to manage typical disruptions to things like transport or animal illness by looking for alternatives. Human labor, however, has never historically been in short supply. Tyson and others had never had to think about where to source people. What’s more, the majority of those employed in the industry are migrant workers on short-term visas. As COVID-19 closed borders and shelter-at-home restrictions came into play, those workers who were not ill or quarantined and wanted to work faced additional legal obstacles.
By early May 2020, an novel dilemma had presented itself: How to resolve the human labor bottle-neck in the American food supply chain?
Resolving this crisis on the ground was contingent on two things: understanding the chain to determine where it had broken, and then enacting the mitigation efforts to control the situation and get things moving once more.
With goods and products not in actual shortage, the disruption was clearly centered around the workforce. For Tyson and other players, that meant that mitigation had to focus on the needs and the physical welfare of workers — as well as the mechanisms that would encourage them back to the plants during a pandemic.
Government agencies, NGOs and industry players came together to roll out a raft of sanitary measures at food processing facilities. These included mass COVID-19 testing of workers, providing personal protective equipment and installing plastic sheets inside plants to enhance social distancing measures.
Employees were also offered a premium on their wages as an incentive to return to work.
As a result, the line was restored to around 30 percent of previous output almost immediately — but then things stalled. The full recovery and return to pre-coronavirus productivity took at least two months. Then there was the economic fallout. The cost of the crisis has also run into the hundreds of millions of dollars, with Tyson alone estimated to have footed a bill in excess of $540 million.
And questions remain.
The wage incentives enacted to bring workers back into plants constitute something of an ethical dilemma with complex trade-offs between individuals’ well-being and collective or societal well-being, and the tensions between people’s right to safety and their need to earn an income.
Then there is there is the question of just how much industries like the food industry will actually learn from this crisis.
Prone to great cycles of panic and neglect (in which industry players have spoken volubly about “wake-up calls” after SARS, Hurricane Katrina and more, only to fail to wake up in any meaningful sense), what actual actions will firms proactively take to shore up their supply chains in the face of future disruption?
In March 2021, U.S. President Biden issued a decree: Going forward, America would need far greater flexibility and resilience around essentials such as food and pharmaceutical supplies.
But in reality, building flexibility and resilience into supply chains is hard. And there are two principal reasons for this.
First, these systems are inherently complex, with multiple potential points of failure. Second, resilience comes with trade-offs that can be hard to stomach. When times are good, planning for the unexpected comes with a price tag that has significant implications for pricing and short-term competitive advantage, especially in crowded markets that are not subject to supply management regulation.
That being said, at the macro level, there are measures that policy makers and industry bodies can explore that could fortify supply chains in the event of major disruptions — disruptions that can and do happen, as the COVID-19 pandemic has demonstrated.
Meanwhile, at the individual level, firms might want to do more in terms of really understanding their own supply chains.
In the U.S., the food industry became super efficient and drove down costs. But it did so at the expense of fragility. Following the COVID-19 crisis, it could go down the route of saying, in essence, “This is a necessary trade-off that just needs to be accepted.”
Alternatively, it could ask itself, “Could better visibility of the supply chain actually improve day-to-day operations — even before the next crisis strikes?
The preceding is based on the case Food Supply and COVID-19: Breaking the Chain (Darden Business Publishing) by Vidya Mani, Doug Thomas and Stephen Maiden.
Mani is an authority in retail operations, supply chain risk management and sustainable operations, and illicit flows and counterfeit goods. Her research investigates and establishes the impact of operational decisions on performance under changing marketplace conditions. She studies how firms can make these decisions in a responsible and sustainable manner, specifically in the retail, electronics, oil and gas, and pharmaceutical sectors.
Mani is currently a Franklin Fellow at the Bureau of Democracy, Human Rights and Labor’s Office of International Labor Affairs, which leads the Department of State’s efforts to advance labor rights in U.S. foreign policy. She has also worked with the U.S. Department of Defense to mitigate counterfeit risk in the weapons system supply chain.
Prior to joining the Darden faculty, Mani taught at Penn State’s Smeal College of Business and earned her Ph.D. at the University of North Carolina at Chapel Hill.
B.E., MS University; MBA, Indian Institute of Technology; Ph.D., University of North Carolina at Chapel Hill Kenan-Flagler Business School
An expert in supply chain management, Thomas researches production and inventory planning across the extended enterprise, as well as connecting decision models to logistics performance measurement. He is co-founder and chief scientist for Plan2Execute, which provides supply chain software and consulting solutions in warehouse management, transportation management and advanced production and inventory planning.
Prior to joining the Darden faculty, Thomas taught at the Smeal college of Business at Penn State and served as a visiting faculty member at INSEAD and Cornell’s Johnson Graduate School of Management.
B.S., Cornell University; M.S., Ph.D., Georgia Institute of Technology
The Food Supply Chain: Weak Links Amid COVID-19
Share