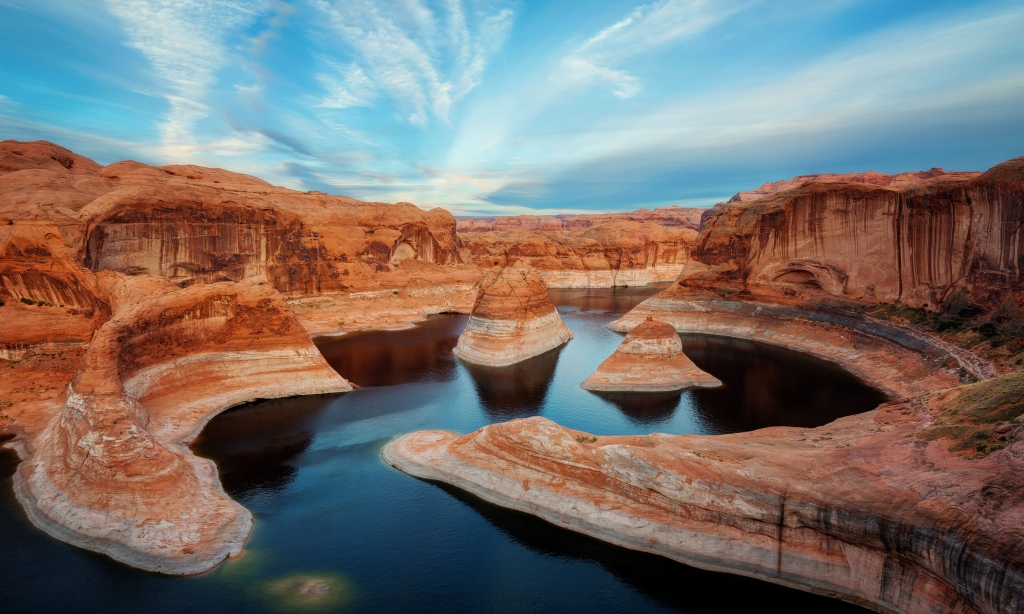
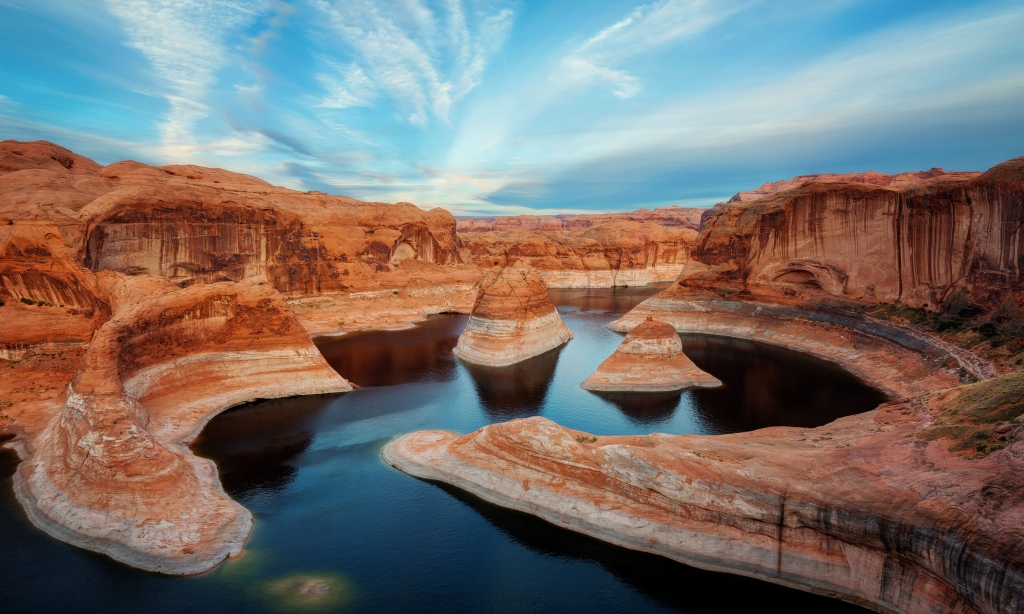
This leap year, why not make the most of the additional day with the subtraction of waste?
Lean practice may be defined as the relentless pursuit of the strategic elimination of waste. Through the continuous refinement of practices and procedures, lean management seeks to produce more goods more quickly while using fewer resources — less factory space, fewer worker movements and fewer assembly steps. Although often associated with manufacturing — Toyota and Danaher are proponents — it is also applied in service settings such as Capital One Financial Corporation. Here we define three types of waste and provide a framework for their identification in production and service processes.[i]
Lean[ii] identifies three types of waste:
Muda has been further divided into seven categories.
Many organizations add an eighth category of muda:
Whether in a service or manufacturing setting, muda, by definition, adds costs to the system in the following ways:
To identify waste in a process, the manager must first “go to the gemba”: Go to the shop floor to get a firsthand look. Going to the gemba may take time and should consist of observation only, so that any subsequent decision is based on a thorough understanding of the process. Gemba is closely related to the concept of genchi genbutsu: Go and see for yourself. A manager must avoid isolation and limiting information to that supplied by reports, which are one or more steps removed from the gemba.
As Taiichi Ohno, the father of Toyota production, puts it, “Data is of course important in manufacturing, but I place the greatest emphasis on facts.”[iii] Ohno suggested drawing a circle on the floor in which to stand and then observe a process for eight hours to emphasize the discipline and patience the process requires.
Lean practitioners recommend that, at the initial phase of a waste audit, waste should be listed as observed; root causes or counter measures need not be identified. Suggestions and improvements should be made and brainstormed in conjunction with future activities.
This post is adapted from the technical note Looking for Muda (Darden Business Publishing), prepared by Darden Professor Elliott N. Weiss and alumnus Harry “Mac” Russell (MBA ’07), which includes a tool for conducting a muda audit.
[i] Because of lean’s roots in the Toyota Production System, many of the terms are of Japanese origin.
[ii] In keeping with its less is more ethos, the lean philosophy has come to be represented by the word itself, sometimes capitalized.
[iii] Jeffrey Liker, The Toyota Way (Columbus, OH: McGraw-Hill, 2003), 226.
Weiss is a top authority in many aspects of manufacturing, including inventory control, manufacturing planning and scheduling, manufacturing project management, materials management, service industry operations, total productive maintenance and lean systems.
Weiss is the author of numerous articles in the areas of production management and operations research and has extensive consulting experience for both manufacturing and service companies in the areas of production scheduling, workflow management, logistics, lean conversions and total productive maintenance.
B.S., B.A., MBA, Ph.D., University of Pennsylvania